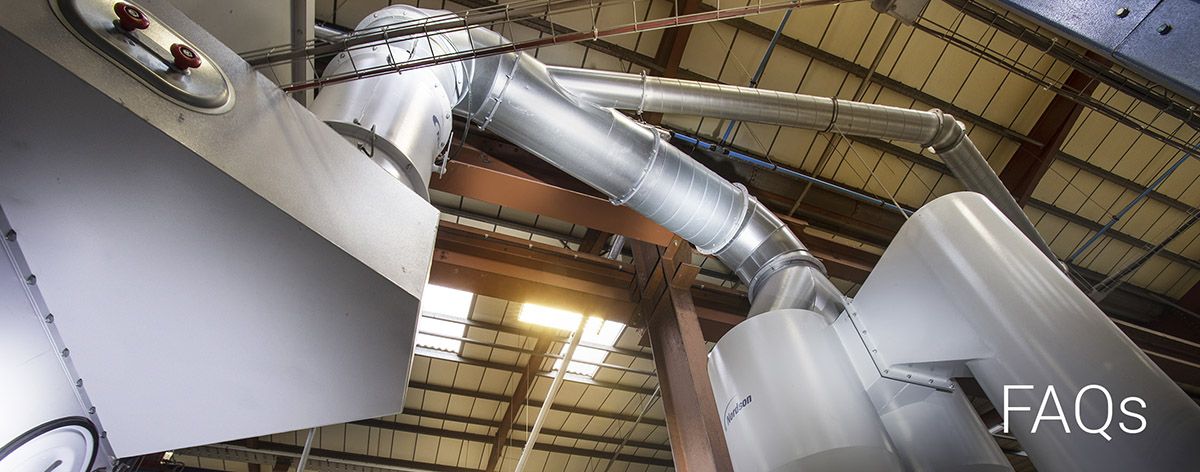
FAQ’s
Polyester powder coating gives an attractive, striking finish and is very popular with good reason. The polyester resin cured at high temperature forms a smooth, hard-wearing coat, with excellent edge coverage and gloss retention. There is an extensive range of colours to choose from, which are highly resistant to fading in direct sunlight.
Polyester powder coating is a great choice for projects based outdoors. The long-term abrasion resistant properties are particularly suited to architectural metalwork, roller-shutter doors, shop-fittings, handrails, garden and leisure equipment, plus many other applications.
There are alternatives to polyester powder coating depending on the nature of your project. For indoor applications, epoxy coating can provide a good quality, thick finish, but it is not really suitable for outdoor use. Nylon coating has a glossy, tough finish, and is used where resistance to oils and solvents is key. Nylon is often used in the food industry because of its non-contaminating nature, and is also used for service vehicles and stadium seating. Thermoplastic polymer alloy is a more costly coating used in the water industry, and sometimes for fencing and play equipment.
Kestrel Powder Coating specialises in polyester powder coating only. Polyester is the most commonly applied coating because of its versatility and a large choice of colours and finishes.
Harsh environments have the potential to affect the finish in the long-term. These include surroundings with airborne debris (e.g. sand), intense direct sunlight, industrial and marine locations, and acidic or alkaline conditions. Problems such as fading, erosion and peeling can occur in such environments, but may be minimised or avoided with sufficient planning together with your coater. Without due consideration of the surrounding environment, the problems mentioned can be rectified, but your coater will not be liable and an on-site sprayer may prove costly.
Regular cleaning will help preserve the finish. The surrounding environment will determine the method and frequency of cleaning required.
If your product will be subject to harsh environments as described, you should make your powder coater aware of this before placing an order. It may be that an alternative to powder coating is more appropriate depending on your requirements and budget. Some powder coaters offer a ‘marine guarantee’ lasting for a limited time against the more challenging elements. A marine guarantee involves much more than simply coating to a greater thickness. The coater and the powder supplier work with the customer to produce an in-depth report of the project, typically gathering the following details: |
|||
|
|||
Not all coaters can offer a marine guarantee, so it is best to check this before ordering from a particular coater. |
Architects can get their information from many sources, even retail outlets and D.I.Y. stores. The colour codes supplied might not be accurate, or colours may be referred to by name such as ‘Racing Green’ or ‘Poppy Red’. Using name descriptions is risky as several different colours can have the same name but vary in shade.
We can send you a colour swatch for choosing colours from our extensive range. With a proper colour code, we are able to establish the availability of the powder.
If you want to provide a colour sample, we can work with our powder suppliers to match your colour exactly. The contract name can sometimes help as particular contracts will use known colours.
At Kestrel Powder Coating we will do our utmost to get the powder colour you require, and in the shortest time possible.
This does not necessarily mean bad news. Non-standard colours can be made to order. You will need to allow more time in such cases as the powder may take several days to formulate, or may have to be imported from abroad.
There is usually a premium surcharge for non-standard colours and finishes. The powder supplier might only manufacture the powder in large batches of 60-100 kilos for example, so the cost has to reflect this. If you intend to order larger quantities, there may be a cost reduction if you let us know in advance.
If you are asked for a non-standard finish in a given colour, it may be worth checking to see if any of the standard finishes for that colour are acceptable first. This can be a much cheaper option than getting a non-standard made up. The standard powder is likely to be available quicker too.
Please provide us with a paper order and keep a copy. That way, everyone will have the information to hand when it is needed. Ideally, your order should contain as much of the following information as possible:
- Order number – This is essential for both customer and supplier during processing and afterwards.
- Colour and finish – Specify the colour, preferably using a colour code, and indicate the finish as matt, satin, or gloss.
- Contract reference – If your order matches an existing contract, please give details.
- Condition of your material – State if the material been anodised, stripped, or if it is already coated. You must notify us if your material has been damaged in any way, or if it has a polyamide filler. All of these factors can ultimately affect the finish.
- Date your order is required – Mark as urgent only if necessary, otherwise let us know the date your coated material needs to be ready. This gives us chance to schedule the coating, order any powder, and arrange for transport in good time.
- Any special requirements – Specify if the material is to be coated all over or only on certain surfaces, identifying clearly which ones. If you want a thicker coating than normal, state the figure, e.g. 90 microns. Also, let us know if you want the material to be stripped first, or thermally broken after coating.
- Expected order cost – We can provide quotations promptly on request.
To keep your coated material looking good, regular cleaning plays an important part. In normal environments, the coating should be washed using a soft cloth or sponge, and warm, soapy water. A solution of water and mild detergent is recommended, e.g. 5% Teepol solution.
For harsher environments and if the project has been properly planned with your coater and the correct measures taken, the powder supplier’s or coater’s own cleaning guidelines for the project will apply.
Where the atmosphere is that of a rural or normal urban environment, the period between cleaning can be up to 9 months. If heavier soiling occurs, then more frequent cleaning is recommended, e.g. in industrial environments, the period should not be more than 3 months. How often the material should be cleaned also depends on the standard of appearance required, and the need to remove any deposits that can cause damage with prolonged contact with the coating.
In no circumstances must you use abrasive cleaners, nor any cleaner containing ketones, esters or alcohol.
It’s a good idea, and sometimes a requirement of the powder supplier, to keep a record of when and how your powder coated material is cleaned.